工場設備の設計段階から保守管理・メンテナンスを計画することで
工場の稼働率を安定させます。
工場設備の安定稼働は製品製造で最重要です。機器の故障や突発的なトラブルによる生産ラインの停止は、売上や修理費用の損失だけでなく、お客様の信頼も失ってしまいます。
そこで大切なのは、日頃からしっかりと点検や部品交換や修理を行い、トラブルを最小限に抑えることです。
的確なメンテナンスは設備の耐用年数も延長させられることから、計画的な保守管理・メンテナンスは設備の安定稼働だけでなく、
【製品のコスト削減・品質向上・安定供給】の実現にも貢献します。
工場設備の安定稼働、保守管理・メンテナンスで
こんなお悩みがありましたら、ご相談ください!
- 自社で保守管理やメンテナンスの人材を確保できない
- 設備異常の原因を掴むのに時間がかかり、適切な修理ができない
- 工場設備の性能を安定させたい
- 設備設計の段階から保守管理の計画を立てて稼働後のリスクをなくしたい
- 保守管理・メンテナンスのノウハウがないので専門家に依頼したい
- 工場設備の定期的なケアで耐用年数を延ばして長寿命な生産ラインを構築したい
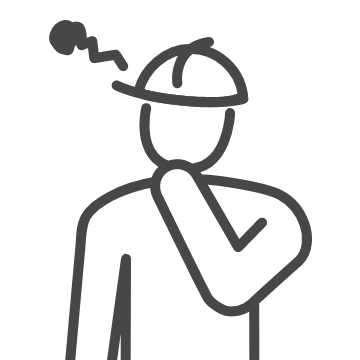
工場設備の安定稼働のポイント
設計段階から保守管理・メンテナンス計画を提案することで
安定稼働を実現。お客様にも喜ばれています。
01
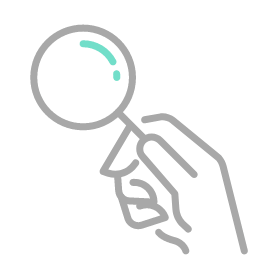
現場の調査・把握
・条件や要求能力の把握
・経験を踏まえた将来予測
・日常点検や定期点検
02
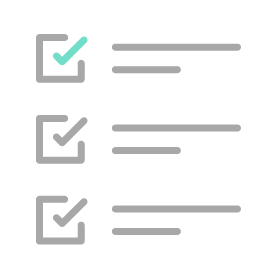
提案・運用計画
・複合的な分析やコンサル
・維持管理が容易な設計
・計画的な保守管理提案
03
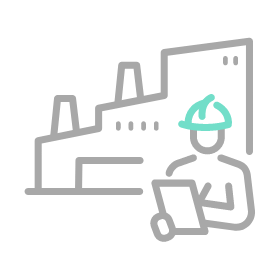
施工・納入
・幅広い設備工事
・安全で確実な施工
・メンテナンス対応
04
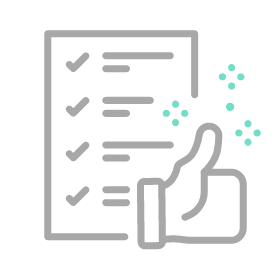
トラブル対応
・突発的なトラブル対応
・機器や部品の劣化調査
・故障状況の原因把握
- 保守管理・メンテナンスでお困りの方
- 「稼働中の設備について相談をしたい」
「新設備導入の保守管理・メンテナンス計画をつくりたい」など、まずはお気軽にご相談ください。
工場設備の計画的な保守管理・メンテナンスのメリット
メリット01
- 設備の異常箇所やパフォーマンス低下を早期発見できる
- 設備の保守管理計画でこまかにチェックすることで、設備異常や不調を早期発見。設備異常による生産への影響を最小限に止める。大きなトラブルを未然に防ぐことにつながります。
メリット02
- メンテナンスコストをトータルで削減
- 日々しっかりと点検やメンテナンスを行うことでトラブル要因となりそうな箇所を早期発見し適切に対処できます。
必要な劣化や不調箇所のみ対応するため、余計な部品の在庫を抱えることもなく、計画的にメンテナンスが行えます。トラブル発生からの事後対応に比べ、メンテナンスにかかる時間やコストの負担をトータルで削減することができます。
メリット03
- 生産ラインを止めない。生産性向上と品質安定で不良率を削減
- 何らかの故障やトラブルが原因で生産ラインが止まってしまうということは、品質にも影響があり生産効率も落ちてしまいます。設備の点検やメンテナンスを適切に行い、常に設備を良好な状態に維持することで高効率かつ不良率の低い生産ラインが構築できます。
メリット04
- 設備のパフォーマンスを最大化。耐用年数もアップ
- 定期的にメンテナンスすることで設備をずっとパフォーマンス高く維持します。
メンテナンスの中でさまざまなケアを行うことで設備の耐用年数も延長し、長寿命な設備になります。
メリット05
- 緊急時にも早く正確にトラブルの原因を突き止め対処できる
- 保守管理計画に基づき、設備の点検やメンテナンスを行うことで、設備異常の発生しやすい箇所や生産ライン固有のトラブル要因がわかってきます。こうした設備稼働のノウハウを蓄積することで、大きなトラブルを察知し回避できるようになります。また、万が一突発的なトラブルが発生した場合も迅速に対応できます。
メンテナンスメニュー
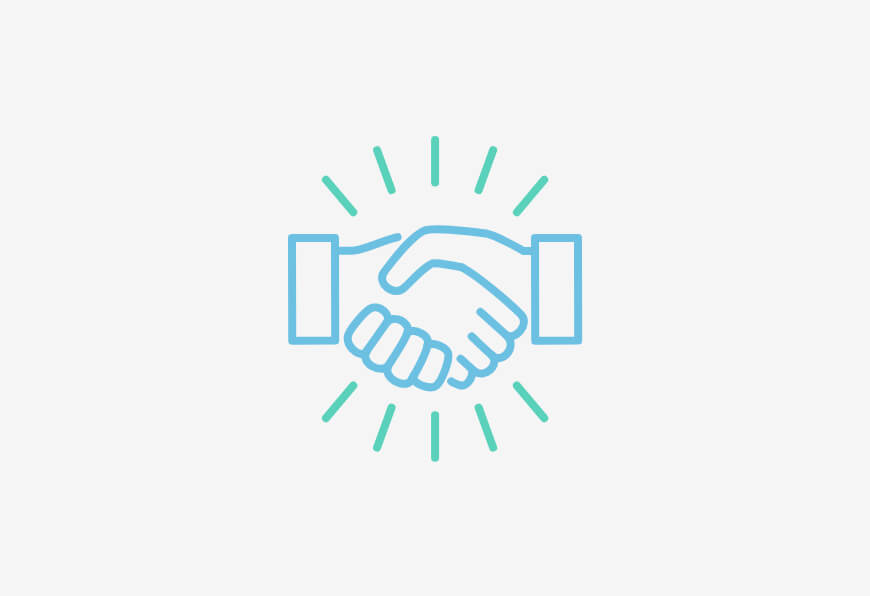
- 定期巡回メンテナンス
- お客様のニーズに合わせたメンテナンスサービスを設定。契約に基づき、当社技術スタッフがお客様施設を定期的に訪問し、運転・維持管理を実施させていただくのが定期巡回メンテナンスサービスです。 ご要望によりあらゆるパターンに対応させていただきますのでお気軽にご相談ください。
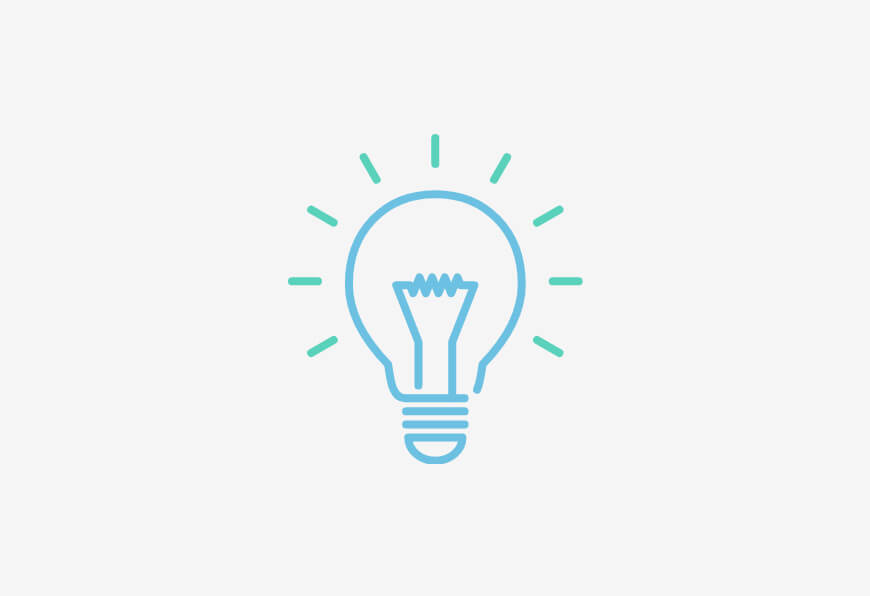
- スポットメンテナンス
- 単発の運転・維持管理をお受けするスポットメンテナンスサービスです。機器本体の不具合はもとより配管設備、計装機器等のメンテナンスも承ります。
万全の保守管理・メンテナンス計画を立てるための3ステップ
01
ヒアリング
お客様の課題やご要望をお伺いします
02
現場や設備の把握
設備の特徴や現場の状況をしっかりと調査します
03
保全計画の作成・実施
定期点検の計画やメンテナンス、修理の計画を作成します